Spis treści:
Efektywne zarządzanie przepływem towarów w magazynie determinuje sukces operacyjny przedsiębiorstwa. Kluczowym elementem tego procesu jest kompletacja zamówień – zespół skoordynowanych działań mających na celu precyzyjne pobranie i przygotowanie jednostek asortymentowych zgodnie ze specyfikacją zamówienia klienta. Sprawność realizacji kompletacji towaru bezpośrednio przekłada się na satysfakcję odbiorcy, koszty operacyjne oraz ogólną wydajność łańcucha dostaw. W niniejszym opracowaniu przyjrzymy się bliżej istocie kompletacji zamówień w magazynie oraz strategiom jej optymalizacji.
Czym jest kompletacja zamówień w magazynie?
Kompletacja zamówień stanowi fundament logistyki magazynowej, obejmując sekwencję czynności od lokalizacji kompletowanych pozycji, poprzez ich pobranie, aż po konsolidację w finalne zamówienie w kompletacji, gotowe do ekspedycji. Nadrzędnym celem zarządzania magazynem jest ciągłe doskonalenie procesu kompletacji, dążąc do minimalizacji nakładów czasowych i zasobowych przy jednoczesnym zachowaniu wysokiej dokładności.
W architekturze współczesnych systemów magazynowych dominują dwa fundamentalne rodzaje kompletacji:
- Kompletacja typu „towar do człowieka”: Charakterystyczna dla środowisk zautomatyzowanych, wykorzystujących zaawansowane systemy kompletacji. W tym modelu, zintegrowane technologie transportują składowane produkty bezpośrednio do stanowiska operatora, eliminując potrzebę jego fizycznego przemieszczania się po strefie kompletacji w magazynie.
- Kompletacja typu „człowiek do towaru”: Tradycyjna metoda kompletacji, w której pracownik odpowiedzialny za kompletowanie zamówień aktywnie porusza się po strefie kompletacji, lokalizując i pobierając poszczególne jednostki towaru zgodnie z wytycznymi zamówienia.
Wybór adekwatnej metody kompletacji oraz implementacja efektywnych systemów kompletacji stanowią strategiczne decyzje, determinujące wydajność i rentowność operacji magazynowych. Zrozumienie specyfiki obu podejść jest kluczowe dla optymalizacji procesu kompletacji w danym przedsiębiorstwie.
Jakie są rodzaje kompletacji zamówień?
W złożonym ekosystemie logistyki magazynowej, kompletacja zamówień może przybierać różnorodne formy, dostosowane do specyfiki operacyjnej i strategicznych celów przedsiębiorstwa. Fundamentalnym rozróżnieniem jest podział na kompletację manualną oraz kompletację automatyczną. Poniższa tabela przedstawia kluczowe aspekty porównawcze obu tych podejść:
Kryterium | Kompletacja Manualna | Kompletacja Automatyczna |
---|---|---|
Proces | Pracownicy fizycznie lokalizują i pobierają towary. | Zautomatyzowane systemy kompletacji transportują towary. |
Wymagane zasoby ludzkie | Wysokie zapotrzebowanie na personel magazynowy. | Zredukowane zapotrzebowanie na personel do kompletacji. |
Szybkość kompletacji | Zależna od wydajności pracownika, potencjalnie wolniejsza. | Znacznie wyższa dzięki pracy maszyn i systemów. |
Dokładność | Podatna na błędy ludzkie. | Wysoka precyzja dzięki technologii. |
Elastyczność | Wysoka elastyczność w obsłudze różnorodnych zamówień. | Mniejsza elastyczność w przypadku nietypowych zamówień. |
Koszty inwestycyjne | Relatywnie niskie koszty początkowe. | Wysokie koszty wdrożenia i integracji systemów. |
Koszty operacyjne | Wyższe koszty pracy w dłuższej perspektywie. | Niższe koszty pracy, wyższe koszty utrzymania systemów. |
Skalowalność | Skalowalność ograniczona dostępnością personelu. | Wysoka skalowalność i możliwość obsługi większej liczby zamówień. |
Wykorzystanie przestrzeni | Potencjalnie mniej efektywne wykorzystanie przestrzeni. | Możliwość bardziej gęstego składowania i efektywnego wykorzystania strefy kompletacji. |
Ryzyko błędów | Wyższe ryzyko pomyłek przy kompletacji towaru. | Minimalne ryzyko błędów dzięki automatyzacji procesu kompletacji. |
Kompletacja manualna, jako tradycyjna metoda kompletacji, charakteryzuje się znaczną elastycznością w obsłudze zróżnicowanego asortymentu i specyficznych wymagań klientów. Niemniej jednak, jej wydajność jest silnie uzależniona od efektywności pracy personelu i może być bardziej podatna na błędy. Z kolei kompletacja automatyczna, oparta na zaawansowanych systemach kompletacji, oferuje znaczną poprawę szybkości i dokładności procesu kompletacji. Choć wiąże się z wyższymi kosztami początkowymi, w dłuższej perspektywie może prowadzić do obniżenia kosztów operacyjnych i zwiększenia przepustowości magazynu. Wybór między tymi dwoma rodzajami kompletacji powinien być podyktowany szczegółową analizą potrzeb przedsiębiorstwa, charakterystyką kompletowanych towarów oraz długoterminową strategią rozwoju.
Rodzaje kompletacji zamówień ze względu na miejsce
Analizując proces kompletacji z perspektywy lokalizacji wykonywanych czynności, wyróżniamy dwa podstawowe podejścia: kompletację jednostopniową oraz kompletację wielostopniową. Każda z tych metod kompletacji charakteryzuje się odmienną organizacją pracy i znajduje zastosowanie w zależności od specyfiki operacji magazynowych. Poniższa tabela przedstawia kluczowe różnice między tymi dwoma strategiami:
Kryterium | Kompletacja Jednostopniowa | Kompletacja Wielostopniowa |
---|---|---|
Proces | Wszystkie produkty z zamówienia zbierane podczas jednej ścieżki kompletacyjnej. | Kompletacja towaru odbywa się w kilku etapach lub strefach. |
Organizacja pracy | Jeden pracownik kompletuje całe zamówienie. | Różni pracownicy lub systemy mogą uczestniczyć w kompletacji poszczególnych części zamówienia. |
Zastosowanie | Mniejsze magazyny, ograniczona liczba SKU. | Duże centra dystrybucyjne, szeroki asortyment, złożona struktura magazynu. |
Efektywność | Wysoka efektywność przy prostych zamówieniach i niewielkim asortymencie. | Efektywna przy dużej liczbie zamówień i rozproszonym asortymencie. |
Czas realizacji | Potencjalnie krótszy czas realizacji prostych zamówień. | Czas realizacji może być dłuższy dla pojedynczego zamówienia, ale ogólna przepustowość wyższa. |
Przemieszczanie się | Minimalne przemieszczanie się w przypadku prostych zamówień. | Większe przemieszczanie się między strefami kompletacji. |
Złożoność | Mniejsza złożoność procesu kompletacji. | Większa złożoność organizacji i koordynacji procesu kompletacji. |
Kompletacja jednostopniowa charakteryzuje się tym, że pracownik odpowiedzialny za kompletowanie zamówień zbiera wszystkie wymagane produkty podczas jednej wizyty w strefie kompletacji. Ta metoda kompletacji jest szczególnie efektywna w środowiskach o ograniczonej liczbie indeksów magazynowych (SKU) i mniejszej powierzchni magazynowej, gdzie odległości do pokonania są niewielkie. Z kolei kompletacja wielostopniowa polega na podziale procesu kompletacji na kilka etapów lub przypisaniu różnych części zamówienia do realizacji w odrębnych strefach kompletacji w magazynie. Takie podejście jest kluczowe w dużych centrach dystrybucyjnych z rozbudowaną infrastrukturą i szerokim asortymentem, gdzie optymalizacja ścieżek kompletacyjnych i specjalizacja zadań przyczyniają się do zwiększenia ogólnej wydajności kompletacji towaru. Niezależnie od wybranej metody kompletacji zamówień, nadrzędnym celem pozostaje usprawnienie procesu kompletacji, minimalizacja kosztów operacyjnych, zapewnienie wysokiej dokładności kompletacji produktów oraz finalnie – satysfakcja klienta.
Kompletacja zamówień „towar do człowieka”
Przygotowanie towarów w dalszą drogę w oparciu o koncepcję „towar do człowieka” zakłada wykorzystanie nowoczesnych systemów regałów automatycznych, wyposażonych w rozwiązania takie jak układnice czy przenośniki pojemnikowe bądź paletowe. Korzyści z takiej inwestycji obrazuje Manager ds. sprzedaży w firmie Nedcon, mgr inż. Anna Iwanowicz:
Interesującym przykładem automatyzacji procesów logistycznych jest zastąpienie klasycznych rozwiązań typu supermarket przy produkcji. Często spotkanym schematem jest połączenie regałów paletowych i rolkowych, gdzie na pełnych paletach trzymany jest zapas komponentów, których potrzebuje produkcja. Dolną część regałów stanowią regały rolkowe, z których zgodnie z zasadą FIFO komponenty są wydawane na produkcję.
Problem w tym rozwiązaniu stanowi m.in. konieczność obsługi regałów przez elektryczne wózki widłowe, które potrzebują ok 3000 mm do swobodnych manewrów. Obsługa wózkiem to także ryzyko uszkodzeń mechanicznych oraz konieczność spełnienia licznych wymogów BHP, które mają zminimalizować ryzyko, np. upadku palety z wysokości.
Co udałoby nam się osiągnąć, gdybyśmy usprawnili proces poprzez odejście od ciężkich i mało zwrotnych wózków widłowych, umieszczając w to miejsce robota? Wyeliminujemy wówczas szereg zagrożeń, związanych z ryzykiem uszkodzeń mechanicznych, kosztownego dozbrajanie regałów w celach bezpieczeństwa czy ryzyko końcówek serii czy braku komponentów, o czym będzie informował nas sam system. Rozwiązanie to pozwoli nam zoptymalizować dostępną przestrzeń, ominąć wiele przeszkód i usprawnić cały proces kompletacji!
Korzyści z inwestycji w nowoczesne systemy magazynowe podkreśla również Konrad Potomski, partner systemu z firmy Loopstore, będący twórcą rozwiązania BOXss. Które branże zyskają najwięcej na zastosowaniu nowoczesnych regałów automatycznych?
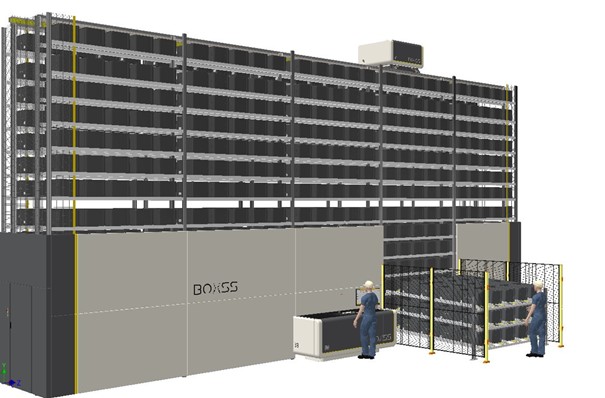
Powyższe rozwiązanie można zastosować w branży produkcyjnej oraz wszędzie tam, gdzie zachodzi potrzeba dostarczania i buforowania części potrzebnych do montażu. Do kategorii tej należy zaliczyć branżę automotive oraz inne sektory, w których odbywa się seryjny montaż, wymagający stałego dopływu części oraz zapasu produkcyjnego. Rozwiązanie to sprawdzi się tam, gdzie znajduje się dużo jednostek SKU i mamy do czynienia z dużym obszarem składowania oraz dużą liczbą linii kompletacyjnych na godzinę.
W przypadku kompletacji 1:1, gdzie każde zlecenie realizowane jest osobno, ludzie spacerujący po podłodze uzyskują około 40-80 linii na godzinę. W przypadku multi-order-picking wydajności te kształtują się zazwyczaj w okolicy 100-150 linii na godzinę. Szacuje się, że w przypadku wartości rzędu ponad 150 linii na godzinę, opłaca się wdrożyć rozwiązanie „towar do człowieka”.
Oczywiście, zastosowanie kompletacji „towar do człowieka” nie wynika tylko z wydajności, lecz również z powierzchni i wysokości składowania. Dla operacji manualnych wykorzystuje się zabudowę do wysokości 2-2,5 m lub antresole. Ograniczona wysokość składowania, która nie przekracza 2,5 m sprawia, że składowanie towarów do kompletacji zajmuje dużą powierzchnię. Problem ten częściowo rozwiązują antresole, lecz wtedy mamy do czynienia z koniecznością pokonywania kilku poziomów.
W obu przypadkach operator musi przejść dziennie dziesiątki kilometrów. To wszystko wpływa na zmęczenie i spadek wydajności kompletacji. Co więcej, osoby kompletujące zamówienia muszą być dobrze zorientowane w ułożeniu towarów na magazynie, żeby wiedzieć, gdzie co się znajduje.
Oczywiście, istnieje możliwość wyszkolenia pracownika – pracodawcy mierzą się jednak z dość dużą rotacją na tego typu stanowiskach, co wiąże się z ciągłym szkoleniem nowoprzyjętych. System „towar do człowieka” eliminuje wyżej wymieniony problem, ponieważ rolą operatora jest tylko pobrać element z pojemnika i odłożyć do pojemnika kompletacji.
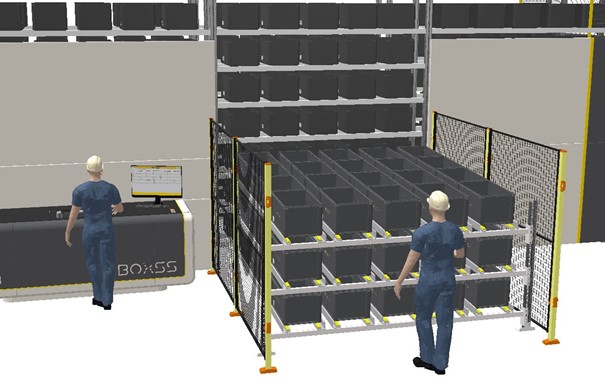
Zarówno miejsce pobrania, jak i odłożenia towaru jest wskazywane przez komputer oraz elementy świetlne, dzięki czemu wyręcza operatora i ogranicza ryzyko popełnienia błędu do minimum. W rozwiązaniu tego typu, szkolenie nowoprzyjętych pracowników jest szybsze i sprowadza się tylko do przeszkolenia z podstawowej obsługi stacji GTM, dzięki czemu istnieje możliwość częstszej rotacji pracowników w strefach kompletacji. Ma to również ogromne znaczenie w przypadku sezonowych pików, gdzie na krótki okres potrzebna jest większa ilość kompletujących – podczas gdy w normalnych warunkach niezbędny byłby cykl szkoleń, a magazyn nie funkcjonowałby przy maksymalnej możliwej wydajności, w przypadku GTM nie ma tego problemu.
Kompletacja zamówień na zasadzie „człowiek do towaru”
Kompletowanie zamówień w oparciu o regułę „człowiek do towaru” polega na przemieszczaniu się pracowników po magazynie i zbieraniu towarów uwzględnionych w zamówieniach. Istnieje kilka metod kompletacji zamówień w oparciu o tę regułę – różnią się one od siebie m.in. wymaganym stopniem zautomatyzowania magazynu.
- pick and pack – najprostsza i najbardziej podstawowa metoda kompletowania zamówień, oparta o samodzielne pobieranie jednostek z poszczególnych regałów,
- pick by light – system zarządzania magazynem podświetla lampki bądź diody nad regałami, zawierającymi przedmiot zamówienia,
- put to light – kompletacja przy pomocy wykorzystującego ekrany systemu informatycznego, który wskazuje miejsce, w których znajdują się dane towary oraz pokazuje ich docelowe miejsce.
Pięć kluczowych kroków do optymalizacji procesu kompletacji zamówień
Efektywna i szybka kompletacja zamówień w magazynie jest fundamentem optymalizacji kosztów operacyjnych oraz kluczowym wyróżnikiem konkurencyjnym, szczególnie w dynamicznie rozwijającym się sektorze e-commerce. W branży, gdzie czas realizacji zamówienia bezpośrednio wpływa na decyzje zakupowe klientów, usprawnienie procesu kompletacji staje się priorytetem. Oto pięć praktycznych kroków, które pozwolą znacząco zwiększyć efektywność kompletowania zamówień:
- Standaryzacja procedur kompletacji i szkolenie personelu:
- Wprowadzenie jednolitych i precyzyjnych instrukcji dotyczących metod kompletacji w całym obiekcie magazynowym.
- Regularne szkolenia pracowników w zakresie obowiązujących procedur, efektywnego wykorzystania narzędzi i systemów kompletacji, a także zasad bezpieczeństwa.
- Zapewnienie ciągłego doskonalenia umiejętności personelu w celu minimalizacji błędów i skrócenia czasu kompletacji towaru.
- Maksymalizacja wykorzystania przestrzeni magazynowej:
- Optymalne zagospodarowanie dostępnej powierzchni składowania poprzez zastosowanie odpowiednich systemów magazynowych, takich jak regały wysokiego składowania, systemy przepływowe czy karuzelowe.
- Inteligentne rozmieszczenie asortymentu z uwzględnieniem częstotliwości rotacji (kompletowania), gabarytów towarów oraz logicznego powiązania produktów często zamawianych razem.
- Implementacja systemów zarządzania magazynem (WMS) w celu efektywnego monitorowania i alokacji miejsc składowania.
- Implementacja dopasowanego systemu składowania:
- Wybór systemu składowania (np. regały paletowe, półkowe, przepływowe, automatyczne) dostosowanego do specyfiki przechowywanych towarów, ich wielkości, wagi oraz częstotliwości kompletacji.
- Wykorzystanie etykietowania i czytelnego oznakowania lokalizacji w celu szybkiej identyfikacji kompletowanych produktów.
- Regularna analiza i optymalizacja układu magazynu w celu skrócenia ścieżek kompletacji i eliminacji wąskich gardeł.
- Inwestycje w technologie wspomagające kompletację:
- Wdrożenie urządzeń i technologii przyspieszających proces kompletacji, takich jak skanery kodów kreskowych, terminale mobilne, wózki kompletacyjne z podnoszoną platformą, systemy głosowe (voice picking) czy systemy świetlne (pick-to-light/put-to-light).
- Rozważenie inwestycji w zaawansowane systemy kompletacji automatycznej, takie jak roboty magazynowe czy automatyczne systemy transportu wewnętrznego, w zależności od skali działalności i budżetu.
- Zapewnienie płynnego przepływu towarów i minimalizacja braków:
- Wdrożenie efektywnego systemu zarządzania zapasami w celu monitorowania stanów magazynowych i prognozowania popytu, minimalizując ryzyko braków towarów, które mogą prowadzić do opóźnień w kompletacji zamówień.
- Optymalizacja procesów przyjęcia i rozładunku towarów w celu zapewnienia ciągłości dostaw i uniknięcia przestojów w procesie kompletacji.
- Regularna analiza przyczyn braków i wdrożenie działań korygujących w celu zapewnienia dostępności kompletowanych produktów.
Implementacja tych pięciu kroków, dostosowana do specyfiki danego przedsiębiorstwa, znacząco przyczyni się do usprawnienia procesu kompletacji, redukcji kosztów operacyjnych oraz podniesienia poziomu satysfakcji klientów poprzez szybszą i bardziej precyzyjną realizację zamówień.
Optymalizacja kompletacji zamówień – inwestycja w przyszłość Twojego magazynu
W dynamicznym środowisku współczesnej logistyki magazynowej, gdzie presja na szybką i efektywną realizację zamówień stale rośnie, proces kompletacji często staje się wąskim gardłem operacji. Czy zauważasz, że kompletowanie zamówień w Twoim magazynie pochłania więcej czasu i zasobów niż kiedykolwiek wcześniej? Wzrost wolumenu zamówień, różnorodność asortymentu czy przestarzała infrastruktura magazynowa mogą znacząco obniżać wydajność i generować niepotrzebne koszty.
Nie pozwól, aby nieefektywna kompletacja towaru hamowała rozwój Twojego przedsiębiorstwa. Skorzystaj z wiedzy i doświadczenia ekspertów Nedcon Silesia. Pomożemy Ci zidentyfikować obszary wymagające optymalizacji i zaprojektujemy system magazynowy idealnie dopasowany do specyfiki Twojej działalności. Nasze innowacyjne rozwiązania w zakresie regałów magazynowych i systemów kompletacji pozwolą Ci stworzyć optymalną przestrzeń składowania, która zagwarantuje oczekiwaną wydajność, zwiększy przepustowość procesu kompletacji i znacząco zredukuje koszty operacyjne.
Dołącz do grona ponad 1000 renomowanych marek, które zaufały profesjonalizmowi Nedcon i przekonały się o realnych korzyściach płynących z nowoczesnego i inteligentnie zaprojektowanego magazynu.
Zainwestuj w przyszłość swojej logistyki!
Skontaktuj się już dziś z naszym zespołem specjalistów Nedcon Silesia, aby omówić indywidualne potrzeby Twojej firmy i otrzymać spersonalizowaną ofertę na optymalizację kompletacji zamówień. Przekonaj się, jak wiele możesz zyskać dzięki nowoczesnemu podejściu do kompletacji w magazynie. Zoptymalizuj swój proces kompletacji z Nedcon Silesia i zyskaj przewagę konkurencyjną!