Spis treści:
Automatyzacja magazynu staje się coraz bardziej popularnym kierunkiem rozwoju logistyki i zarządzania łańcuchem dostaw. Przedsiębiorstwa na całym świecie dostrzegają korzyści płynące z optymalizacji procesów magazynowych, takich jak zwiększenie efektywności, redukcja kosztów i zmniejszenie ryzyka błędów ludzkich. Wprowadzenie automatyzacji może być kluczowym krokiem na drodze do osiągnięcia przewagi konkurencyjnej na rynku.
Ale jak rozpoznać, kiedy jest najlepszy moment na inwestycję w takie technologie? W niniejszym artykule przyjrzymy się różnym aspektom automatyzacji procesów magazynowych, omówimy dostępne rozwiązania oraz pomożemy ocenić, czy automatyzacja jest odpowiednia dla Twojego biznesu.
Czym jest automatyzacja procesów magazynowych?
Automatyzacja procesów magazynowych, czasami nazywana automatyzacją systemów, polega na digitalizacji ręcznych operacji, takich jak gromadzenie danych inwentaryzacyjnych, i ich integracji z systemami oprogramowania, takimi jak bazy danych lub systemy ERP (Enterprise Resource Planning). Automatyzacja obejmuje ekosystem kodów kreskowych i bezprzewodowych skanerów, które wprowadzają i śledzą dane, przekazywane później do scentralizowanego repozytorium, co pozwala na lepsze zarządzanie informacjami.
Jakie korzyści przynosi automatyzacja procesów magazynowych?
Najprościej ujmując, automatyzacja procesów oznacza zastosowanie specjalistycznego sprzętu oraz systemów magazynowania i wyszukiwania do realizacji zadań, które wcześniej były wykonywane przez pracowników z użyciem prostych narzędzi.
Automatyzacja magazynu pozwala na:
- usprawnienie prostych procesów,
- zmniejszenie liczby potrzebnych pracowników lub
- zwiększenie wydajności magazynu przy tej samej liczbie zatrudnionych.
Zautomatyzowany magazyn ogranicza ręczne zadania, które spowalniają przepływ towarów, co prowadzi do zwiększenia efektywności. Automatyzacja magazynu pozwala na usprawnienie prostych procesów, zmniejszenie liczby potrzebnych pracowników lub zwiększenie wydajności magazynu przy tej samej liczbie zatrudnionych. Zautomatyzowany magazyn ogranicza ręczne zadania, które spowalniają przepływ towarów, co prowadzi do zwiększenia efektywności.
Rodzaje automatyki magazynowej: Od prostych systemów po zaawansowane rozwiązania
Automatyzacja fizyczna obejmuje szeroką gamę technologii, które mogą usprawnić działanie magazynu. Wśród najważniejszych rodzajów automatyki magazynowej wyróżniamy:
Zautomatyzowane technologie pakowania
Automatyczne pakowanie, etykietowanie oraz sortowanie produktów pozwala na szybsze przygotowanie zamówień do wysyłki. Systemy takie jak wagi kontrolne, linie pakujące czy etykieciarki są kluczowe dla magazynów e-commerce, gdzie liczy się szybkość i dokładność realizacji zamówień.
Roboty i systemy zautomatyzowanego transportu
Te systemy obejmują wykorzystanie robotów, które automatyzują transport wewnątrz magazynu. Są to kosztowne rozwiązania, które najlepiej sprawdzają się w większych systemach magazynowych oraz centrach dystrybucyjnych.
AGV (Automated Guided Vehicle)
Zautomatyzowane pojazdy bez kierowcy, które przemieszczają się po wyznaczonych trasach, dostarczając towary do wyznaczonych stref.
AMR (Autonomous Mobile Robot)
Autonomiczne roboty mobilne, które korzystają z zaawansowanych algorytmów, aby samodzielnie planować trasę. Realizują koncepcję dostarczania towarów do osoby (GTP – Goods To Person).
Zautomatyzowane systemy transportu poziomego (przenośniki)
Przenośniki to systemy, które pozwalają na przemieszczanie ładunków poziomo w magazynie. Stosowane są do transportu pojemników, kartonów lub palet na krótkie i średnie odległości, co znacząco poprawia przepływ materiałów i redukuje konieczność ręcznego przenoszenia.
Układnice (ASRS – Automatic Storage and Retrieval System)
Systemy te są używane do automatycznego składowania i pobierania ładunków. ASRS mogą być stosowane zarówno do ładunków standardowych, jak i niestandardowych, przy użyciu odpowiednich jednostek nośnikowych. Standaryzacja ładunków pozwala na optymalizację kosztów, ponieważ upraszcza obsługę oraz minimalizuje potrzebę dodatkowych urządzeń peryferyjnych, takich jak przenośniki czy skanery.
Systemy zarządzania magazynem (WMS)
Połączenie fizycznej automatyzacji z systemem zarządzania magazynem pozwala na koordynację operacji w czasie rzeczywistym, co wpływa na większą przejrzystość procesów i umożliwia efektywniejsze zarządzanie zasobami. WMS współpracuje z technologiami takimi jak przenośniki, AGV, AMR czy ASRS, zapewniając synchronizację działań.
Do najpopularniejszych systemów automatyki magazynowej należą karuzele, windy pionowe, układnice oraz zautomatyzowane pojazdy transportowe (AGV i Transfercar). Istnieje również kategoria systemów obejmujących przenośniki, które przenoszą i kierują materiały do kolejnych etapów procesu, np. sortowania, pakowania czy ważenia. Automatyzacja tych procesów jest szczególnie istotna w magazynach logistycznych nastawionych na obsługę e-commerce.
Automatyzacja magazynu w praktyce
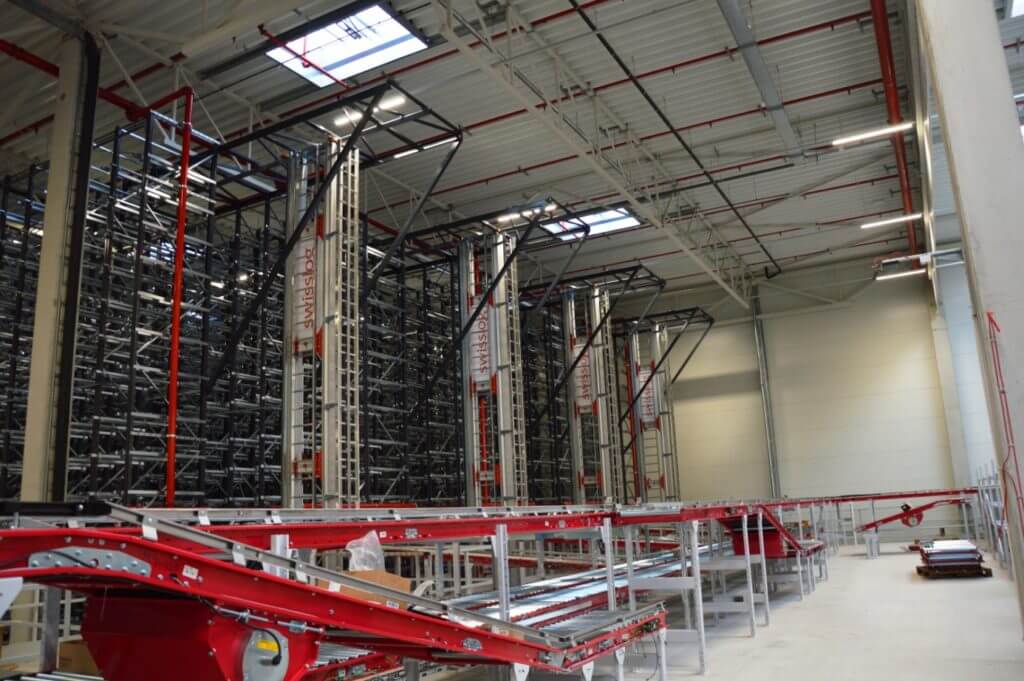
Najlepiej zilustruje to powyższy przykład: wymieniony system składowania ASRS może być używany ze standardowymi ładunkami, jak również niestandardowymi ładunkami, wtedy jako nośniki używa się dodatkowe zestandaryzowane jednostki, na których umieszczane są kartony czy inne nietypowe towary użytkowane w magazynie. Standardowe ładunki upraszczają obsługę oraz pozwalają zoptymalizować koszty urządzeń peryferyjnych takich jak przenośniki, bramki skanujące czy urządzenia do kontroli zawartości nośników.
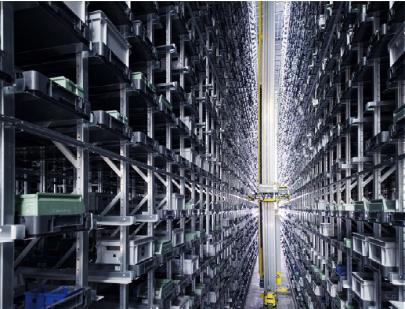
8 sygnałów, że Twój magazyn potrzebuje automatyzacji
Automatyzacja procesów magazynowych nie zawsze jest koniecznością, jednak istnieją pewne sygnały, które mogą świadczyć o potrzebie jej wdrożenia. Jeśli którykolwiek z poniższych punktów dotyczy Twojego magazynu, warto rozważyć inwestycję w nowoczesne technologie:
- Duża ilość powtarzalnych operacji transportowych – Jeśli w magazynie przemieszcza się duża ilość ładunków w powtarzalnych ścieżkach, automatyzacja transportu wewnętrznego może znacząco poprawić efektywność.
- Ograniczona przestrzeń magazynowa – Gdy brakuje miejsca do składowania towarów, a standardowe wózki lub systemy podnoszenia nie są w stanie podnieść towarów wystarczająco wysoko, automatyzacja może pomóc w lepszym wykorzystaniu dostępnej przestrzeni.
- Brak wartości dodanej w procesach – Jeśli procesy magazynowe, takie jak przyjmowanie, układanie, pobieranie i wysyłka, nie dodają wartości do towaru, a jedynie powtarzają te same operacje, automatyzacja może zminimalizować koszty związane z ręcznym wykonaniem tych czynności.
- Konieczność zachowania wysokiej dokładności – W magazynach, gdzie dokładność jest kluczowa, automatyzacja może pomóc uniknąć kosztownych pomyłek, które mogą prowadzić do uszkodzeń ładunków lub błędów przy wydaniach.
- Rosnąca potrzeba kontroli jakości – Jeśli konieczne jest zwiększenie liczby pracowników tylko po to, aby ponownie sprawdzić dokładność zamówienia, automatyzacja procesu kontroli może znacząco zmniejszyć koszty.
- Zbyt czasochłonne i pracochłonne procesy – Jeśli obecne procesy magazynowe wymagają dużej ilości czasu i pracy, co wpływa na spadek wydajności, automatyzacja może znacznie przyspieszyć te operacje.
- Niedokładne stany magazynowe – Jeśli dane dotyczące stanów magazynowych są często niedokładne, wprowadzenie systemów automatycznego gromadzenia danych może poprawić jakość informacji i umożliwić lepsze zarządzanie zapasami.
- Wzrost kosztów obsługi zamówień – Gdy koszty obsługi pojedynczego zamówienia rosną ze względu na niewydolność procesów lub załogi, automatyzacja może pomóc w optymalizacji kosztów operacyjnych.
Automatyka magazynowa – przegląd najpopularniejszych systemów
Najbardziej popularne systemy automatyki magazynowej mają na celu zwiększenie efektywności procesów magazynowych, poprawę wydajności oraz redukcję kosztów operacyjnych. Wybór odpowiedniego rozwiązania zależy od rodzaju magazynowanych towarów, wielkości magazynu oraz specyficznych potrzeb danej firmy. Poniżej przedstawiamy najczęściej stosowane systemy automatyzacji:
Wśród najbardziej popularnych systemów automatyki magazynowej warto wyróżnić:
- Karuzele magazynowe – Pozwalają na efektywne składowanie i łatwy dostęp do małych części. Wykorzystuje się je szczególnie tam, gdzie jest potrzeba szybkiej kompletacji drobnych elementów.
- Windy pionowe (VLM – Vertical Lift Module) – Systemy te umożliwiają składowanie na wysokość, co pozwala oszczędzać miejsce i jest szczególnie przydatne w magazynach o ograniczonej powierzchni.
- Automatyczne systemy magazynowania i wyszukiwania (ASRS) – W tym układnice oraz mini-układnice. Są idealne do magazynów o dużym wolumenie, gdzie precyzja oraz efektywność są kluczowe.
- Zautomatyzowane pojazdy transportowe (AGV i Transfercar) – Pojazdy te są wykorzystywane do transportu materiałów w obrębie magazynu. AGV (Automated Guided Vehicle) i Transfercar sprawdzają się w dużych centrach dystrybucji, gdzie konieczne jest szybkie i bezbłędne przemieszczanie towarów.
- Przenośniki – Przenośniki są używane do transportu materiałów między różnymi stanowiskami, np. do sortowania, pakowania czy ważenia. Są szczególnie popularne w magazynach logistycznych obsługujących e-commerce.
Automatyka magazynowa dostarcza różnorodne rozwiązania, które można dostosować do potrzeb konkretnej firmy. Wybór odpowiedniego systemu zależy od skali działalności, rodzaju magazynowanych towarów oraz celów, które firma chce osiągnąć.

Automatyzacja procesów magazynowych w branży e-commerce – kluczowe czynniki decyzyjne
Automatyzacja w magazynach e-commerce to złożony proces, który wiąże się z wieloma aspektami, takimi jak efektywność, koszty oraz obsługa klienta.
Kluczowe czynniki, które mogą wpłynąć na decyzję o automatyzacji magazynu e-commerce:
- Zwiększenie szybkości kompletacji zamówień oraz ich wysyłki – Automatyzacja pozwala na szybkie kompletowanie zamówień i ich wysyłkę, co jest kluczowe w przypadku dużej liczby zleceń, szczególnie w okresach szczytowych.
- Obsługa większej liczby zamówień w krótszym czasie przy niższych kosztach per zamówienie – Automatyzacja procesów magazynowych pozwala na zwiększenie liczby obsługiwanych zamówień bez konieczności zatrudniania większej liczby pracowników. Dzięki temu obniża się koszt jednostkowy realizacji zamówienia.
- Ograniczenie błędów przy kompletacji zamówień – Wykorzystanie technologii takich jak systemy pick-to-light czy roboty kompletacyjne zmniejsza liczbę błędów przy kompletacji zamówień, co wpływa na zadowolenie klienta i redukuje koszty związane z reklamacjami.
- Pozyskiwanie danych do analizy (np. sezonowość, stany magazynowe) – Automatyzacja zapewnia dokładne dane na temat stanów magazynowych, rotacji towarów oraz sezonowości sprzedaży, co pozwala na lepsze planowanie i zarządzanie zasobami.
- Obsługa wielu kanałów sprzedaży – Automatyzacja magazynu ułatwia zarządzanie zamówieniami pochodzącymi z różnych kanałów sprzedaży, takich jak e-commerce, sklepy stacjonarne czy platformy sprzedażowe, co pozwala na lepsze koordynowanie przepływu towarów.
- Efektywne zarządzanie zwrotami – W branży e-commerce zwroty są nieodłącznym elementem działalności. Automatyzacja procesów zwrotów, takich jak przyjęcie towaru, inspekcja i ponowne wprowadzenie do magazynu, pozwala na szybsze i bardziej efektywne zarządzanie zwrotami, co zmniejsza ich koszty.
7 praktycznych sposobów na zwiększenie wydajności zautomatyzowanego magazynu
- Rozbicie lokacji paletowych tzw. podłogowych na „dwa poziomy” za pomocą nowej poprzeczki lub dodając drugą SKU pionowo podzieloną na jednej palecie. Spowoduje to utworzenie pół-paletowego kompletu, co zapewni pobieranie dwóch SKU ze zbliżonych lokacji.
- System odprowadzający opróżnione kartony SKU ze stacji wzdłuż przenośnika, aby uniknąć bałaganu.
- Unikanie ponownej obsługi czyli np. użycie opakowania wysyłkowego – a nie plastikowego pojemnika do kompletacji.
- Używanie wag liniowych do wykonywania kontroli jakości według wagi produktu, a nie liczenia produktów już spakowanych.
- Wstępne oznakowanie kartonów wysyłkowych przed ich złożeniem lub rozpoczęciem odbioru.
- Wbudowanie urządzenie do układania kartonów, urządzeń do ich zamykania czy wypełniania, aby zwiększyć prędkość linii.
- Wykorzystanie pracy dorywczej w celu minimalizacji kosztów.
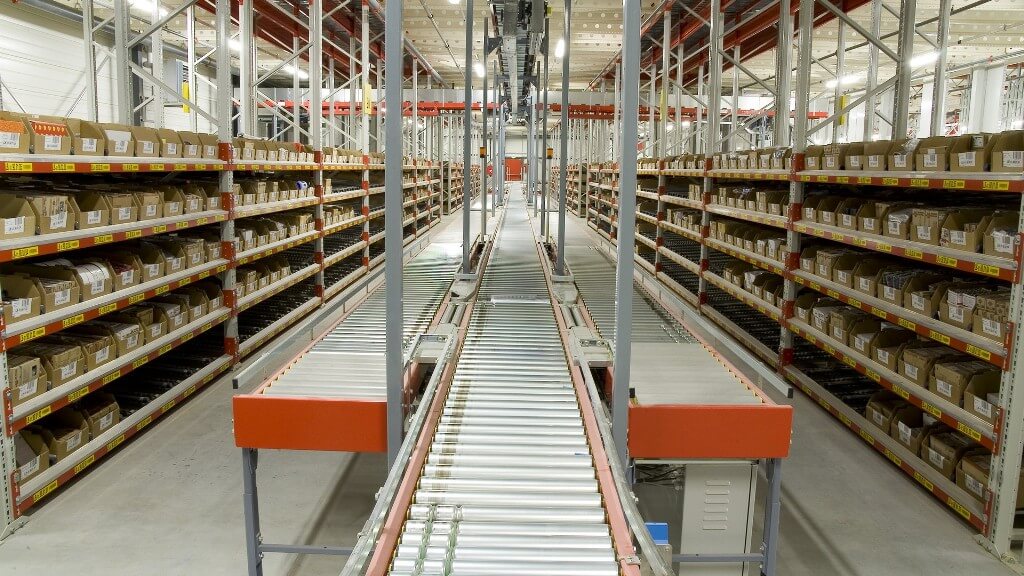
Automatyzacja magazynu: Koszty, zwrot z inwestycji i długoterminowe korzyści
Korzyści z automatyzacji magazynu
Automatyzacja pozwala na podniesienie efektywności magazynowania do poziomów niemożliwych do osiągnięcia przy wyłącznym udziale pracy ludzkiej. Urządzenia przejmują powtarzalne i czasochłonne zadania, dając pracownikom możliwość skupienia się na bardziej złożonych procesach wymagających interwencji człowieka. Dzięki automatyzacji możliwe jest także:
- Redukcja błędów – Automatyzacja minimalizuje ryzyko błędów ludzkich, które mogą się zdarzać podczas ręcznego zarządzania magazynem.
- Zwiększenie przepustowości – Automatyczne systemy mogą pracować szybciej niż ludzie, co przekłada się na większą przepustowość operacji magazynowych.
- Lepsze zarządzanie przestrzenią – Systemy automatyczne pomagają zoptymalizować sposób składowania towarów, co prowadzi do lepszego wykorzystania dostępnej przestrzeni magazynowej.
- Zmniejszenie kosztów pracy – Zautomatyzowane systemy pozwalają na redukcję liczby pracowników potrzebnych do wykonywania powtarzalnych zadań, co obniża koszty operacyjne.
Koszty automatyzacji magazynu
Wdrożenie automatyzacji wiąże się z początkowymi kosztami inwestycyjnymi, które mogą obejmować zakup urządzeń, instalację infrastruktury oraz integrację z istniejącymi systemami informatycznymi. Należy wziąć pod uwagę:
- Koszty zakupu sprzętu – Inwestycja w zautomatyzowane układnice, przenośniki, roboty oraz systemy zarządzania magazynem (WMS) może być znacząca.
- Koszty wdrożenia – Proces wdrożenia automatyzacji może wymagać zaangażowania specjalistów oraz dostosowania istniejącej infrastruktury magazynowej.
- Koszty utrzymania – Automatyzacja wiąże się również z kosztami utrzymania sprzętu oraz ewentualnymi kosztami serwisu i napraw.
Zwrot z inwestycji w automatyzację
Zwrot z inwestycji (ROI) w automatyzację magazynu zależy od wielu czynników, takich jak skala operacji, typ przechowywanych towarów oraz poziom automatyzacji. W zależności od wdrożonego rozwiązania, zwrot z inwestycji może nastąpić już po 12-16 miesiącach, ale w większości przypadków jest to okres od 5 do 10 lat. Czynniki wpływające na zwrot z inwestycji obejmują:
- Skala operacji – Im większy magazyn, tym szybciej można zauważyć oszczędności wynikające z automatyzacji.
- Koszty pracy – W regionach, gdzie koszty pracy są wysokie, automatyzacja szybciej przynosi zwrot z inwestycji.
- Wydajność operacyjna – Zwiększenie wydajności i redukcja błędów bezpośrednio wpływają na poprawę rentowności.
Rozwiązania częściowej automatyzacji
W sytuacji, gdy nie jesteś jeszcze gotowy na pełną automatyzację, możesz rozważyć wprowadzenie rozwiązań, które mogą być skalowane w miarę wzrostu potrzeb Twojego magazynu:
- Automatyczne gromadzenie danych – Wprowadzenie technologii, takich jak skanery kodów kreskowych i RFID, pozwala na lepsze śledzenie przepływu towarów w magazynie.
- System zarządzania magazynem (WMS) – Wdrożenie systemu WMS umożliwia optymalizację procesów magazynowych, poprawę dokładności stanów magazynowych oraz lepsze planowanie operacji.
Częściowa automatyzacja może być pierwszym krokiem do pełnego zautomatyzowania magazynu i pozwala na stopniowe przystosowanie się do nowych technologii, jednocześnie minimalizując ryzyko i rozkładając koszty w czasie.
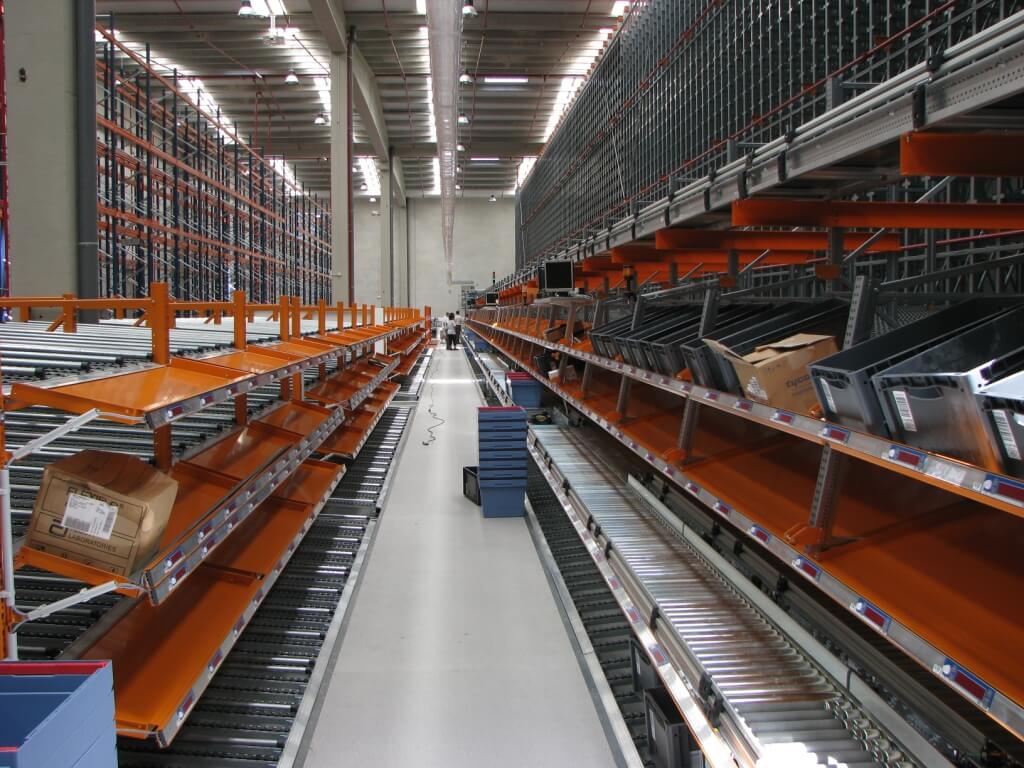